SAI
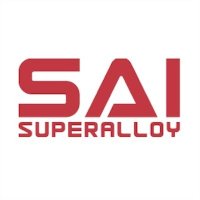
SAI Super Alloy
SuperAlloy Industrial Company Ltd. (SAI), founded in 1994, is an international company who specializes in engineering and manufacturing lightweight metal products for predominantly the Automotive industry, forged aluminum wheels for luxury and sports automobiles super car. The company is headquartered in Taiwan, R.O.C – with sales and support offices located in United States of America, United Kingdom, Germany and Netherland.
By 2002 SAI was awarded GM’s Tier 1 certification and became supplier of well-known automotive brand such as Rolls-Royce, BMW, BENZ, FERRARI, PORSCHE, FORD, CHRYSLER, TOYOTA, JAGUAR and so on.
The Challenge!
SAI's factory primarily utilizes modern large-scale machinery such as molding machines, CNC machines, polishing machines, robots, convey or belts, and material handling equipment. However, it cannot export data from the machinery to do report or analysis, which leads to the following problems:
-
Inaccurate cost calculations due to system can not track the data of production.
-
Production plan delayed because no real-time notifications from the machinery. This includes urgent production orders, machine malfunctions, process changes, and unexpected situations.
-
Issues with controlling and monitoring machinery at each production station.
-
Lack of real-time tracking and display for production processes.
-
Increased yield rate problems because no data for production root causes.
Additionally, SAI requires to create Product Resume to demonstrate compliance as global production standards and regulatory certification requirements. This also ensures customer confidence the ability of aluminum wheels to world-class standards factory's.
After using ciMES
SAI has installed the ciMES system from ARES to increase efficiency all production process. They chose 5 modules that are suitable for factory as follows:
After implementing the ciMES system, work processes improvement as follows:
-
Real-time tracking of Work-in-Progress (WIP) based on Part#, Routing, Station, Equipment, Material, and QC.
-
Linked data between robots, conveyor belts, and PLCs to enhance production efficiency.
-
Tool, equipment, or mold preparation data can be linked to the ciMES system, enable to recheck with Work Orders (WO) and ensuring that the products are produced correctly as specified standards.
-
Real-time QC data and SPC (Statistical Process Control) graphs.
-
Able to display information about the production process environment, such as strength, pressure, electricity, and more, through IoT (Internet of Things) and accurately sends data back to Work Orders (WO).
-
Installed electronic labels and E-SOP (Electronic Standard Operating Procedures) makes the production process easier to work with and verify.
-
Provides management data 5 topics : employees, machinery, materials, environmental certification, and inspection methods.
-
The system has received certification from AEC & IATF (International Automotive Task Force) in the Automotive industry's quality control.
Contact for more information : 0633253640 or 02-6863000 ext. 3042
Email: support@aresth.co.th